News
Prusa Research Begins Manufacturing 3D Printers...
[Newark, Delaware, 2nd July, 2024] - Prusa Research, a leading global developer and manufacturer of 3D printers based in Europe, has announced that it will start producing its popular 3D...
Prusa Research Begins Manufacturing 3D Printers...
[Newark, Delaware, 2nd July, 2024] - Prusa Research, a leading global developer and manufacturer of 3D printers based in Europe, has announced that it will start producing its popular 3D...
Printed Solid hires Chief Sales and Marketing O...
Newark, DE., February 20, 2024. Printed Solid is proud to announce and welcome Chris Pelesky as the Company’s Chief Sales & Marketing Officer. Chris will be responsible for sales team...
Printed Solid hires Chief Sales and Marketing O...
Newark, DE., February 20, 2024. Printed Solid is proud to announce and welcome Chris Pelesky as the Company’s Chief Sales & Marketing Officer. Chris will be responsible for sales team...
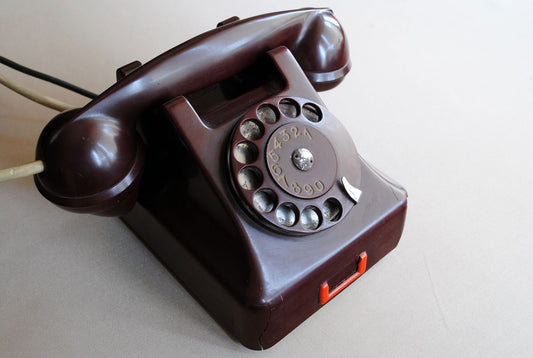
We are going to phone it in for RMRRF April 22-...
The Rocky Mountain RepRap Festival is April 22-23 in Loveland, Colorado and it will be a great show with all sorts of vendors and users and makers. So if you...
We are going to phone it in for RMRRF April 22-...
The Rocky Mountain RepRap Festival is April 22-23 in Loveland, Colorado and it will be a great show with all sorts of vendors and users and makers. So if you...
With the announcement of MK4 why should you sti...
With the announcement of the MK4 by Prusa we are very excited at Printed Solid and we are already working with Prusa Research to try and get inventory in house...
With the announcement of MK4 why should you sti...
With the announcement of the MK4 by Prusa we are very excited at Printed Solid and we are already working with Prusa Research to try and get inventory in house...
Why our prices are different from ordering from...
We have already paid the customs, duties, tariffs. Anything purchased from Printed Solid ships from our USA based warehouse in Delaware so those international charges have already been accounted for....
Why our prices are different from ordering from...
We have already paid the customs, duties, tariffs. Anything purchased from Printed Solid ships from our USA based warehouse in Delaware so those international charges have already been accounted for....
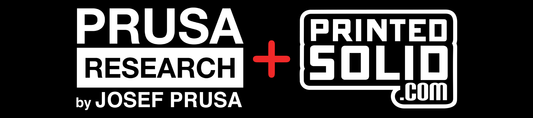
Prusa Research acquires Printed Solid Inc.
Newark, Delaware— 5/16/2022 — Prusa Research acquires Printed Solid Inc.to expand direct sales and support into the USA.
Prusa Research acquires Printed Solid Inc.
Newark, Delaware— 5/16/2022 — Prusa Research acquires Printed Solid Inc.to expand direct sales and support into the USA.