News
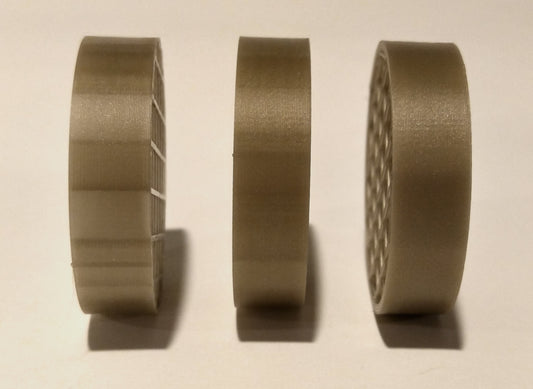
A Solid Foundation For: Infill - Definitions
Sometimes, infill is visible through the surfaces of a print. Even when the plastic is opaque enough not to show the infill by translucence, the infill pattern can sometimes be...
A Solid Foundation For: Infill - Definitions
Sometimes, infill is visible through the surfaces of a print. Even when the plastic is opaque enough not to show the infill by translucence, the infill pattern can sometimes be...
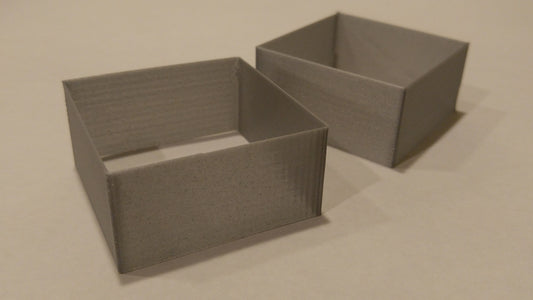
A Solid Foundation for: High-Quality Corners
There are two main opposing types of errors that can produce poor corners: ringing and corner swell. To achieve high-quality corners, certain parameters must be matched to the printer’s physical...
A Solid Foundation for: High-Quality Corners
There are two main opposing types of errors that can produce poor corners: ringing and corner swell. To achieve high-quality corners, certain parameters must be matched to the printer’s physical...
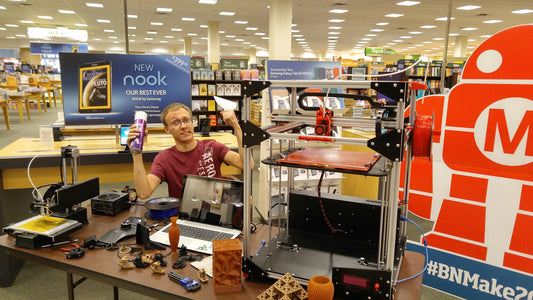
Daniel Halvorson - New Guest Blogger
If you are active on any number of Facebook 3D Printing groups, there's a good chance you've had a positive interaction with Daniel Halvorson. I'm active on a lot of...
Daniel Halvorson - New Guest Blogger
If you are active on any number of Facebook 3D Printing groups, there's a good chance you've had a positive interaction with Daniel Halvorson. I'm active on a lot of...