E3D
E3D V6 Hot End - 1.75mm
E3D V6 Hot End - 1.75mm
Couldn't load pickup availability
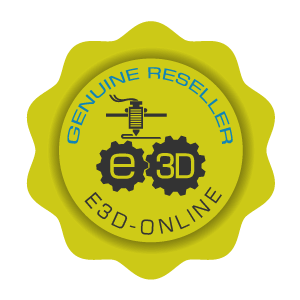
Released in May 2014, the E3D V6 has really become the gold standard premium 3D Printer hotend upgrade.
What’s in the box:
- Metal parts (heatsink, heater block, heat break, 0.4mm nozzle)
- Embedded bowden coupling and bowden clip (1.75mm universal and 3mm bowden versions only)
- Polycarbonate fan shroud
- Short length of 2mmID X 4mmOD PTFE tube (1.75mm universal only)
- 12V 30W heater cartridge (24V available on request)
- 12V fan (24V available on request)
- Semitec 100kohm thermistor, embedded in a metal cylinder for trouble free installation.
- Assorted fasteners for mounting
- 750mm bowden tubing and threaded bowden adapter (Bowden versions only)
- A silicone sock to insulate the hot end and nozzle
Considering this vs other hot ends? Check out this extremely informative review and installation guide. Also, check out this list of printer specific installation guides.
Information and description of some features directly from the E3D Blog:
Decreasing size
Our first mission was to decrease bulk – the heatsink and the fan comprise much of the size of the hotend, with bowden fittings in the relevant versions also adding a fair bit of size up top.
The first target for slashing size was the heatsink. We’ve moved to a smaller diameter heatsink that is also shorter in length. By switching to a very thin cutting tool we were able to get more fins in less space and so retain sufficient surface area on the heatsink to still get good cooling out of a smaller heat sink. It’s also 30% lighter than the previous heatsink.
A comparison between the v5 heatsink (top) and the v6 (bottom).
The next vector for reduction in size was the fan duct. After much agonising over the merits of printed parts and the cost of tooling up for injection moulding we went for an injection moulded part.
We’re really pleased with how these turned out!
The new ducts are a great deal thinner and less bulky in all directions than the previous printed versions. We had these done in polycarbonate resin too which makes them ultra tough and resistant to temperature.
The next area to address was the bowden couplers – we consulted with a specialist in tube coupling solutions and took inspiration from how similar things are achieved in the pneumatics industry. We managed to come across a solution so small that it would fit entirely inside of the hotend! The coupling system we’re using is exactly like the screw-in fittings we’re all used to where a collet holds the tube in place and the tubing can be released easily by simultaneously pushing in the collet and pulling out the tube, just a great deal smaller in size.
Can you see the bowden coupling on the v6 on the left? No? That’s because it is entirely contained inside the heatsink. The small black part is just the collet poking out the top because it’s in the “up” position.
For the 3mm versions the integrated couplers were a tiny bit bigger which meant that we had to deviate from our previous groovemount dimensions slightly, but because the previous coupler sat in that space anyway it shouldn’t make much difference in terms of mounting considerations.
Quite the difference!
A Convenient Side Effect
Because the new bowden coupling system sits entirely within the hotend this now means that there is no need for 2 separate 1.75mm products for Bowden users and Direct users. Instead we have a 1.75mm Universal product that has the internal couplers installed. Direct users just use a short length of tubing to line the filament down into the hotend, and bowden users can simply use a longer piece of tubing with a coupler to fix the other end to their extruder.
Making it Easier
Kapton is an amazing space age material that has paved the way for innovations in electronics, aerospace and many other areas in our modern lives. It’s also a total pain in the ass. When done well it works perfectly functionally, it’s just not as clean or easy a process as we would like.
As To deal with the inconvenience of having to remove the fan duct by sliding it either up or down off the heatsink we have designed the new injection moulded duct so that it simply clips into place over the heatsink from the side, with a satisfying snap as it does so.
Improving Performance for Flexible Filaments.
Flexible filaments are amazing and open up a huge range of possibilities for new practical applications in 3D printing, and they’re also just plain fun. However printing them can be really hard work, especially in 1.75mm where the lower diameter of the filament results in a filament that has mechanical properties similar to that of a wet noodle. To make matters worse many of these filaments also have a certain amount of surface tack, that rubber like grippyness – great for printing things like tyres and grips, terrible when you’re trying to make it slide down an extruder neatly.
To solve this issue we have added the (optional) ability to run PTFE tubing all the way from your hobbed bolt/drive gear to deep down into the hotend.
The PTFE tubing can start right up at the drive system.
The PTFE tubing passes right down through the heatsink
Finally the tubing enters the the heatbreak locating itself in a counterbore at the top of the heatbreak.
The amount of difference this makes when printing 1.75mm flexible filaments is staggering, we went from slow prints at 5-10mm/s that would stop feeding due to buckling with terrible oozing and retract performance to printing at 20-30mm/s with perfect reliability and retractions that were actually very effective at combatting ooze.
Check out our our print of emett’s Rhombic Dodecahedra Chain printed in NinjaFlex!
This mod has several upsides for printing more standard filaments too. Slightly flexible filaments like Nylons also benefit from improved retraction performance. Feeding in a new filament is easier as there is only a single junction where the filament has to cross from the PTFE tubing into the HeatBreak and this junction is extremely concentric and there is next to no gap between the exit hole of the tubing and the entry hole of the heatbreak. Finally friction is reduced across the board due to the PTFE lining for the majority of the filaments travel.
It is worth noting at this point that PTFE is never in any of the heated areas of the hotend and as such we’ve maintained our all-metal high temperature performance with no danger of plastic melting or PTFE liners cooking.
If for some reason you are unable or don’t want to run a tube up into your extruder and just want to use your hotend like back in the good old days that’s fine too, just trim the the PTFE tubing off flush with the top of hotend and carry on.
All of the above applies to the 1.75mm universal product. In 3mm it wasn’t possible to get PTFE right down into the heatbreak which means that a 3mm direct is broadly the same situation as per v5. The good news here is that flexibles are much easier to print in 3mm, which renders the PTFE lining unnecessary.
The 3mm Direct Heatsink
However if you really want some of that PTFE lined goodness in your 3mm hotend then you might look at getting the 3mm Bowden product instead and using it like a direct hotend, it’s much like the 1.75mm Direct hotend in that it uses a coupler that resides entirely within the heatsink and so can be mounted as a direct hotend with the small caveat that it diverges a little from our other groovemounting dimensions to accomodate the larger internal coupler.
The 3mm Direct HeatSink and its embedded coupler
Shortening Heat-Up Times and Increasing Temperature Control Performance.
Our new heater blocks do away with the previous set-screw that locked the heater in place and instead use a radically different approach where the heater block wraps around cartridge and is clamped into place by tightening a screw which physically deforms the heater block so it wraps tightly all the way around the heater for the best possible thermal contact.
The 3mm Direct HeatSink and its embedded coupler
If you look carefully you can the slight deformation of the block.
Next we looked at how we placed the thermistor, the idea here is to have the thermistor be as representative of the temperature of the plastic in the hotend. This means going deep into the block and getting as cozy as possible with the nozzle.
We’re using the same old Semitec 104GT2 thermistor as in v5, which a some people dislike because of it’s small size, while we can appreciate they are ever so slightly harder to work with than their larger cousins they have some tangible benefits. The small glass bead has an extremely fast thermal response, the thermal time constant of the much loved (but now discontinued) Epcos 100K thermistor is 2.5x slower than the Semitec. The second clear advantage the Semitec has over the Epcos is they are much more consistent in their physical size, this means we can place them in a closely toleranced hole for the best thermal contact.
All this adds up to some really tangible gains in temperature control – we can go from a cold start to 200C in 65s and be settled at steady temperature only a few seconds later. Temperature swings are extremely small, less than half a degree.
We’ve kept the same basic thermodynamics from v4 and v5 that involves a super sharp thermal break. We’ve done some deeper thermal analysis of heat flow and temperature gradients surrounding the crucial transition area of the break, but this all simply led us to the conclusion that things were already correct and no changes were needed.
A capture of a thermal simulation of the heatbreak at 250C.
As you can see the hot side is hot, and the cold side is cold.
Addressing Reliability Head On
Although the vast majority of users are printing away hapilly in all materials including PLA we’re still seeing the occasional failure crop up. Most of the time this is something environmental such as a lack of cooling, dodgy filament or configuration issues, however we are seeing the odd user still struggle when they’re doing all the right things and all their problems go away when we replace the hotend.
These problems invariably come down to two components, the HeatBreak and the Nozzle.
The HeatBreak is a critical component as it is where filament makes the transition from a rigid solid to a viscous liquid. When the filament is halfway through these states it can take on a sticky rubbery form that wants to adhere to the HeatBreak, this is particularly true with PLA. If a HeatBreak has a critical imperfection in the areas where the filament is in its sticky state then this can cause jamming.
So after much experimentation we came up with a good, reliable way of ensuring a high quality surface deep into a 2mm diameter hole in stainless steel. This removes any chance for imperfections which plastic in it’s sticky state may cling to.
A view of a heatbreak that has been cut in half to analyse internal surface finish.
We opted to only finish the portion of the HeatBreak that comes into contact with warm filament. The image above demonstrates the new finish on the heated side of the break (left), it is worth noting that in the production version the improved surface extends a good bit further to the right into the cold side of the break in order to account for retractions.
The next area we looked at was the nozzles, 1.75mm Bowden users were experiencing notably more issues than others and thanks to some very in-depth detective work by Michael Hackney this was linked with the length of the small diameter hole in the very tip of the nozzle. If the length of that small diameter hole was reduced then the issue went away. We’ve shortened the length of that final hole in our nozzles in v6 significantly and also upped the tolerances to which that hole length is drilled in order to reduce variance in that crucial dimension.
We have competing theories at E3D about what exactly makes the problem more prevalent among the 1.75mm Bowden users compared to 1.75mm Direct users – remember that the heatbreak and nozzle of the v5 1.75mm Bowden products and the v5 1.75mm Direct are identical and taken from the same batch. What we do know for sure is that the fix works.
Nozzle Specificity and Indentifiability.
While we were in the process of going over the nozzle we thought we’d address making them easily identifiable on a per-size basis. It’s fairly obvious whether a nozzle is 1.75mm or 3mm, but telling the difference between a 0.35mm and a 0.40mm is incredibly hard, and that’s before they get covered in plastic. To that end we have added spots drilled onto the hex flats of the nozzles, the number of which corresponds to a specific size of nozzle. The more dots the bigger the nozzle. We did consider using a binary code, but decided that we didn’t need 64 different sizes of nozzles in the end – maybe one day.
When a nozzle is printing it is not only outputting a stream of plastic, but also flattening it into its final stadium cross sectional shape. The width of this printed track is wider than that of the nozzles small diameter hole, as such the nozzle tip needs to have a flat on it that is at least as wide as the widest sensible track width. Because the widest sensible track width varies depending on the nozzle diameter it logically follows that the tip flat diameter should vary with the nozzle diameter.
Phwwoooar look at that proportional orifice-tip-flat relationship!
This means that with our larger 0.60mm and 0.80mm nozzles you can lay down fatter wider layers than ever before. This is great for large fast printing of super-strong objects, Nylons in particular benefit from being printed from big nozzles. Additionally you can create beautiful very glassy looking objects with big layers of PET type materials like _XT ,T-Glase and Polycarbonate.
Taulman t-glase – Scripted Vase by hakalan.
For our smaller nozzle this means you can get even greater resolution and print smaller details and features in your objects. The smaller tip flat allows you to put down those small features and details without an over sized tip flat smudging the tracks adjacent to what is being printed.
These nozzles are also backward compatible with v5 and v4 so you can use them on existing hotends if you want to get some proportional orifice-tip-flat relationship goodness in your life without swapping out the whole hotend.
This Product has been updated with new variants you now have the ability to directly select your Direct or Bowden and your voltage 12v or 24v.
Added Prusa variant as well this is the 24v Direct Drive kit with a Prusa Heater and Prusa thermistor the Prusa variant is for the MK3 Only.
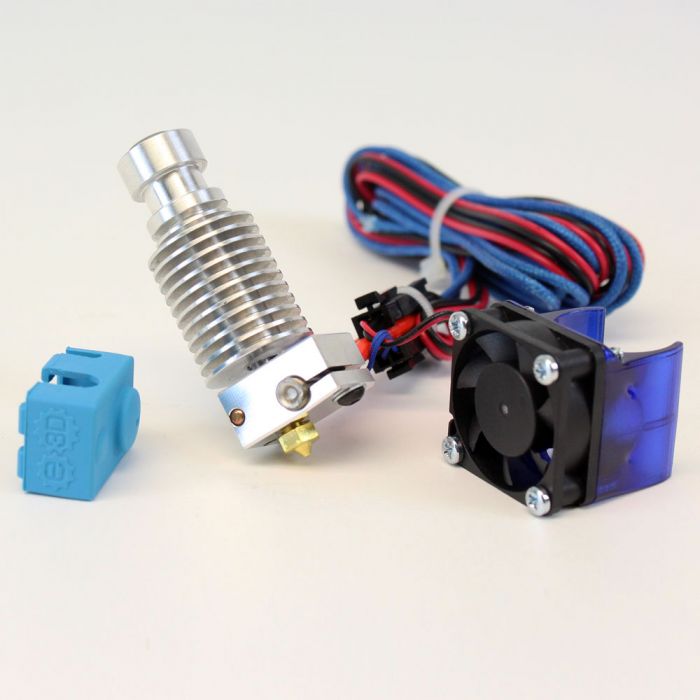
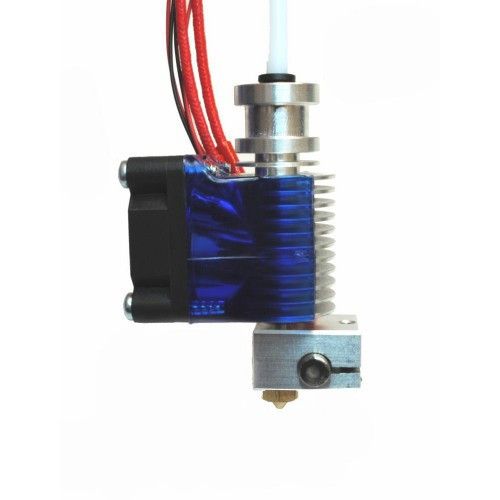



- Reviews
- Questions
- hotend
- Printed Solid
- parts
- printer
- guys
- filament
- Everything
- stock
- instructions
- upgrade

Pretty good upgrade
I did well with the upgrade on a Prusa i3 Mk3+, except for the new type thermistor. I couldn't get a new firmware compiled without a multitude of issues. The guide is outdated, so the instructions are no longer correct regarding changes to configuration.h or configuratioin.adv and with my attempts at hacking it, resulted in compile errors. So, I reverted back to a Prusa thermistor. Also, the fan is pretty cheap. Mine broke a support off when installing it when I pressed on the center of the fan to push it in place. I can say all this in confidence as I have over 30 years experience, including a career with computers and manufacturing electronics. Other then that the updates are worth the while for me. I also have installed bondtech gears and would recommend that update as well.

worked fine for 2 prints....
it worked fine for 2 prints and then the thermistor quit reading. Now I have to find a new one

Great product and super service
Ordered the hotend knowing it is be the standard of hotendsand it was in perfect shape. It was my first time ordering from printed solid and they are awesome. Was delivered in 3 days and shippings was cheap. Also was well packaged and enjoyed the sticker it came with.

E3D V6 Hot end
All parts were included, went together easily and works perfect. Fast shipping (showed up next day!) Looking forward to increasing number of Voron parts.

Best upgrade
When the kit came it came with everything I needed to get it on my printer. It is the best upgrade I have.
- Choosing a selection results in a full page refresh.